The Importance of Air Pressure in Laser Cutting Process Analysis
During the laser segmentation process, the pressure of the auxiliary gas has a significant impact on the segmentation results. Laser cutting machine concentrates light into a high-density beam, which is transmitted to the working surface and generates sufficient heat to melt the material. In addition, high-pressure gas coaxial with the beam directly removes the molten metal, thereby achieving the purpose of cutting. This indicates that laser cutting processing is fundamentally different from mechanical processing of machine tools. The so-called laser cutting machine is to use the energy released when the laser beam is irradiated onto the surface of the workpiece to melt and evaporate the workpiece, in order to achieve the purpose of cutting and engraving. It has the characteristics of high precision, fast cutting, not limited to cutting patterns, automatic typesetting to save materials, smooth cutting, and low processing costs. It will gradually improve or replace traditional metal cutting process equipment. The auxiliary gas must have sufficient pressure to thoroughly remove the waste residue generated during segmentation. Generally, when segmenting thicker workpieces, the pressure should be reduced slightly, and the residue adhering to the workpiece will damage the segmentation edge.
Increasing gas pressure can advance the segmentation speed, but after reaching a larger value, continuing to increase gas pressure will actually cause a decrease in segmentation speed. Laser cutting machine concentrates light into a high-density beam, which is transmitted to the working surface and generates sufficient heat to melt the material. In addition, high-pressure gas coaxial with the beam directly removes the molten metal, thereby achieving the purpose of cutting. This indicates that laser cutting processing is fundamentally different from mechanical processing of machine tools. The so-called laser cutting machine is to use the energy released when the laser beam is irradiated onto the surface of the workpiece to melt and evaporate the workpiece, in order to achieve the purpose of cutting and engraving. It has the characteristics of high precision, fast cutting, not limited to cutting patterns, automatic typesetting to save materials, smooth cutting, and low processing costs. It will gradually improve or replace traditional metal cutting process equipment. The reason for the decrease in cutting speed under high auxiliary gas pressure can be attributed not only to the enhancement of the cooling effect of the hanging action zone by the high airflow velocity, but also to the interference of intermittent shock waves in the airflow on the cooling of the laser action zone. There are uneven pressures and temperatures in the airflow, which can cause changes in the density of the airflow field. This density gradient causes a change in the refractive index within the field, resulting in the focusing of the beam energy and causing refocusing or beam divergence. This interference can affect the melting efficiency and sometimes alter the pattern structure, resulting in a decrease in cutting quality if the beam diverges too much. Making the light spot too large can even result in serious consequences such as ineffective cutting.
To avoid adverse effects of high-speed airflow on segmentation performance, it is possible to consider changing the overall pressure distribution within the airflow. Due to this change in airflow pressure distribution, the melting process (gu ò ch é ng) occurs in the central low-pressure zone; And the surrounding high-pressure zone can be increased to sufficient momentum (impulse) to ensure more effective screening of slag. Laser cutting machine concentrates light into a high-density beam, which is transmitted to the working surface and generates sufficient heat to melt the material. In addition, high-pressure gas coaxial with the beam directly removes the molten metal, thereby achieving the purpose of cutting. This indicates that laser cutting processing is fundamentally different from mechanical processing of machine tools. Due to the intermittency of the high-pressure zone, it does not interfere with the speed of light, and the melting efficiency is also improved.
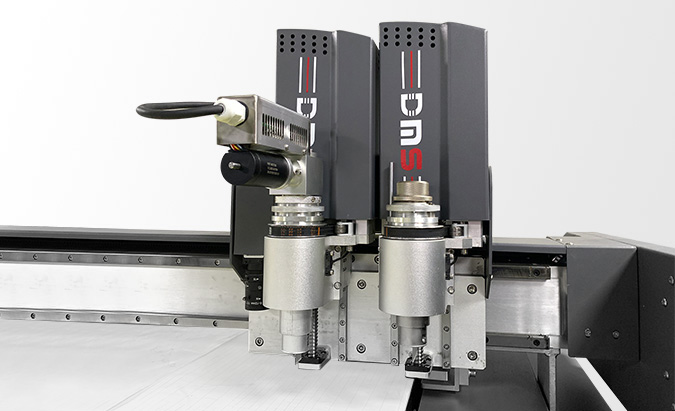